Overvoltage! Billet Flywheels on Mercury V6 Two-Strokes
- Mike Hill
- May 2
- 3 min read
Updated: May 7
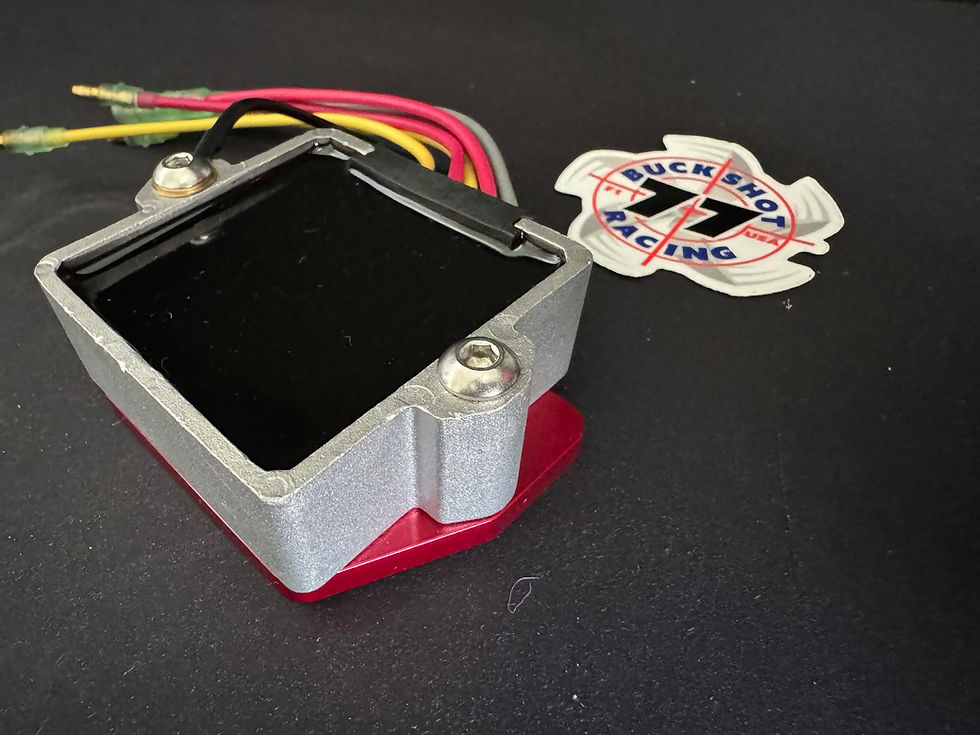
Mercury’s high-performance 2-stroke V6 outboards—particularly the 2.0L, 2.4L, and 2.5L models including the XR2, XR4, XR6, 150, 175, 200, 225 Pro Max horsepower variants, along with race motors like the 260 EFI Offshore, 300 Drag, S3000, and SST120—are built for high-RPM operation, often spinning well beyond 7,200 RPM.
Many of these engines rely on a 16-amp charging system to minimize rotational mass and reduce parasitic drag, critical for maximum throttle response and performance.
However, when these motors are modified with aftermarket billet flywheels containing rare-earth magnets, significant and potentially damaging overvoltage issues can occur—particularly if the charging system remains unregulated.
From the factory, Mercury’s 16-amp stator and flywheel systems used ferrite-based magnets, often referred to generically as ceramic magnets. These magnets were embedded in either a cast steel flywheel or, in the case of factory racing flywheels, a lightweight aluminum version.
While ferrite magnets are relatively corrosion-resistant and cost-effective, they are also brittle, prone to chipping or cracking, especially under the extreme vibrations and thermal cycling typical of high-performance outboard use. Their magnetic output is stable but relatively modest, matching the voltage handling characteristics of the early rectifiers and ignition modules used in these systems.
Modern billet aluminum flywheels used in performance upgrades often replace the original ferrite magnets with rare-earth magnets, such as neodymium. These magnets can produce up to three times the magnetic field strength of the originals.
That increased field density translates directly into higher stator output voltage—a benefit in theory, but one that quickly becomes a liability when used with the unregulated three-post rectifiers that Mercury originally supplied with many of these engines.
In a standard 16-amp system, the stator output at idle might be around 30 volts AC. But at high RPM—especially in the 7,200+ range common with the 260 EFI, Drag, and S3000 platforms—AC voltage can climb beyond 90 volts.
When rectified but left unregulated, this can produce DC charging voltages as high as 15.5 to 17 volts, depending on the battery’s load and condition. Such levels far exceed what most 12V batteries or electronic systems can tolerate.
Overvoltage at this scale has a direct and measurable impact on engine reliability. Batteries begin to gas and boil, especially if they are sealed AGM types, and over time, cells will dry out and fail.
Lithium batteries without a proper Battery Management System (BMS) can enter protection mode or shut down altogether. Deep cycle batteries, though often marketed as "marine-grade," are generally not well-suited for the fast-charge, high-RPM environment of a 2-stroke outboard stator system.
A large, flooded lead-acid starting battery remains the most tolerant of brief overvoltage conditions due to its internal structure and buffering capacity.
But it’s not just the battery at risk. Mercury’s ADI and CDI ignition systems—especially the switchboxes and stator windings—are highly sensitive to excessive voltage.
Consistent exposure to anything above 15 volts DC can cause switchbox overheating, misfires, and eventually catastrophic failure. If voltages in the 16–17V range are observed during operation, the engine should be shut down immediately to prevent ignition or charging system damage.
To resolve this, a combined 20-amp regulator/rectifier is the proven solution. This modern unit performs both rectification and voltage regulation, clamping output safely at approximately 14.4 volts, regardless of engine speed or stator voltage input.
This makes it ideal for use with rare-earth magnet billet flywheels and high-RPM applications. It ensures consistent, safe battery charging and stable voltage delivery to all engine electronics.
The 20-amp regulator/rectifier also offers a direct replacement for a long list of Mercury’s original unregulated rectifier part numbers, including 154-6770, 18-5707, 49184, 62351A1, 62351A2, 70350A1, 70350A3, 72310, 8M0058226, 816770, 816770T, and 9-17100.
Additionally, it replaces Mercury’s older two-wire voltage regulator, part number 88825-A7, used on many 2.4L and 2.5L race engine blocks. To facilitate installation, a billet aluminum mounting bracket is available, designed to bolt directly to the top of the V6 powerhead using factory mounting bosses, maintaining a clean, vibration-resistant, and heat-dissipating install location.
For owners and builders of Mercury 2.0L, 2.4L, and 2.5L high-performance outboards—especially those running billet flywheels and pushing well above 7,000 RPM—the voltage regulation system must match the increased stator output. The original rectifiers were never designed for this much magnetic energy.
Replacing the three-post rectifier with a properly regulated 20-amp unit, and using a compatible bracket that mounts cleanly in place of the original 88825-A7 regulator, is the correct, reliable, and proven approach to modernizing the charging system for these legacy two-stroke powerhouses.
Comments